Additive manufacturing (AM) to produce critical components for a wide range of applications in aerospace with ceramic materials
In recent years, defense and aerospace companies have increasingly turned to additive manufacturing (AM) to produce critical components for a wide range of applications—a trend that is gaining momentum almost as swiftly as the aircraft they design. According to technology advisory firm SmarTech, the aerospace sector ranks as the second largest industry segment utilizing AM, following healthcare. This advanced manufacturing technique, also known as 3D printing, often yields parts that are more durable, aerodynamic, cost-effective, and environmentally friendly compared to those produced by traditional methods.
Why are ceramic materials attractive for aerospace
Ceramic materials, in particular, have become highly attractive for aerospace designs. Since the early 1980s, developers have secured over 8,000 patents related to aerospace-grade ceramics, reflecting the significant investments in research, design, and implementation of these materials. AM ceramics enable the creation of lighter, intricately detailed components with remarkable structural strength, toughness, and resistance to extreme temperatures. Consequently, many aerospace companies are now incorporating ceramics into engine and propulsion systems (such as fuel systems, igniters, nozzles, and rupture disks), electrical components (including antennas and high-voltage feed-through connectors), and structural components (like control systems, struts, and ceramic braking systems).
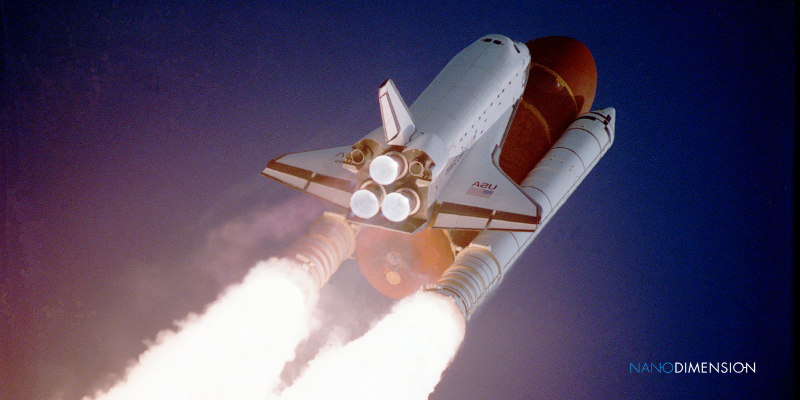
Six factors that play into 3D printed ceramic materials
In the quest to explore the final frontier, the materials used in spacecraft and related technologies play a crucial role in ensuring the success and safety of missions. Among these materials, ceramics have emerged as indispensable due to their unique properties and capabilities. Here’s a look at why ceramic materials are so important for space applications.